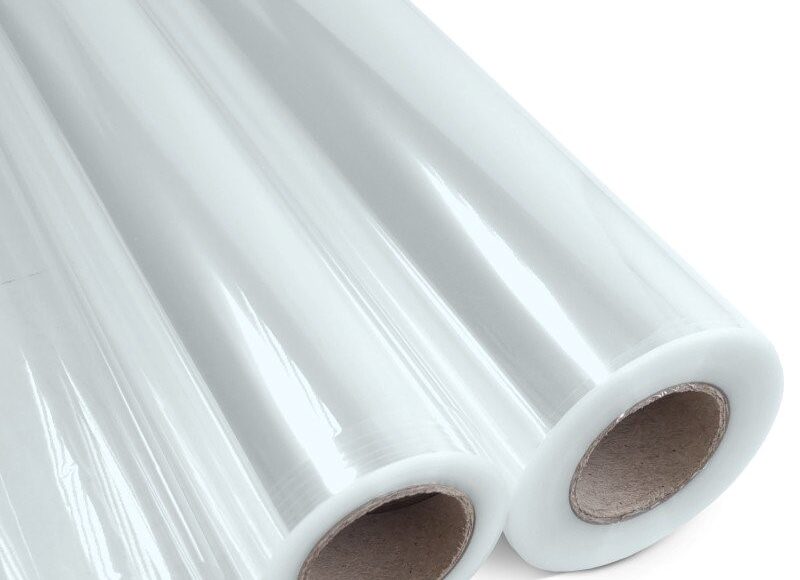
What is Cellophan?
The first flexible film Is cellophane, a thin and transparent sheet made from regenerated cellulose. Its low permeability to air, oils, greases, bacteria, and liquid water makes it useful for food packaging. However, cellophane is highly permeable to water vapor, which can be mitigated by coating it with nitrocellulose lacquer. Uncoated cellophane is resistant, transparent, oil-resistant, and moisture-absorbing
The production process of cellophane begins with “wood.” The “cellulose” obtained from wood is converted into “cellulose hydrate” through a chemical reaction and is then compressed into film. In these conditions, the film is sensitive to liquids. To make it resistant to liquids and moisture, both surfaces are coated with various lacquers (nitrocellulose or PVDC) for use in the packaging industry. Permeability to water vapor and other gases is significantly reduced
Cellophane is used with a copolymer of chloride before polyvinyl, particularly in coating applications with plastic films due to its poor thermal adhesion. Cellophane coated with polymer is resistant to mineral oil
Cellophane is one of the oldest types of film available in three varieties in the market
- P Cellophane (uncoated)
- MS, DMS Cellophane (coated with nitrocellulose, low odor permeability)
- XS Cellophane (PVDC lacquer-coated, low oil and water permeability)
IT was the first transparent flexible material used in packaging goods. In the packaging of many products and both small and large packages, a single layer of cellophane is often insufficient; therefore, two layers of cellophane are used, placed as separate layers on the packaging machine. The two layers of cellophane are bonded together at the sealing points with thermal seals, creating a complete package
Uncoated cellophane is very sensitive to moisture; it equilibrates with the moisture in the air. If it absorbs moisture, it becomes soft; if it loses moisture, it becomes brittle and fragile. Uncoated film does not have stable impermeability characteristics and lacks thermal sealing capabilities. Typically, one or both sides of the cellophane used in flexible laminated packaging are coated with polyvinylidene chloride to maintain a series of consistent properties. Nitrocellulose layers are rarely used as coatings
The thickness of cellophane is determined based on the type of product and requirements. The thinnest thickness typically used for lamination is about 20 microns; a two-layer laminate with adhesive in the form of PVDC-CELLO-PVDC has greater durability than a single layer of the same thickness. Two-layer lamination allows for printing between layers, resulting in greater gloss and protection against ink migration. Laminating cellophane with various BOPP films increases impermeability and toughness; it also enhances stability and durability
The most important consideration when printing on cellophane film is that the film temperature during printing should be 80-90 degrees Celsius. This is because the ink only adheres well to the film surface at these temperatures. Cellophane film, often used for twist wrap packaging, is also utilized after printing in lamination. The highest preference is for lamination with polyethylene