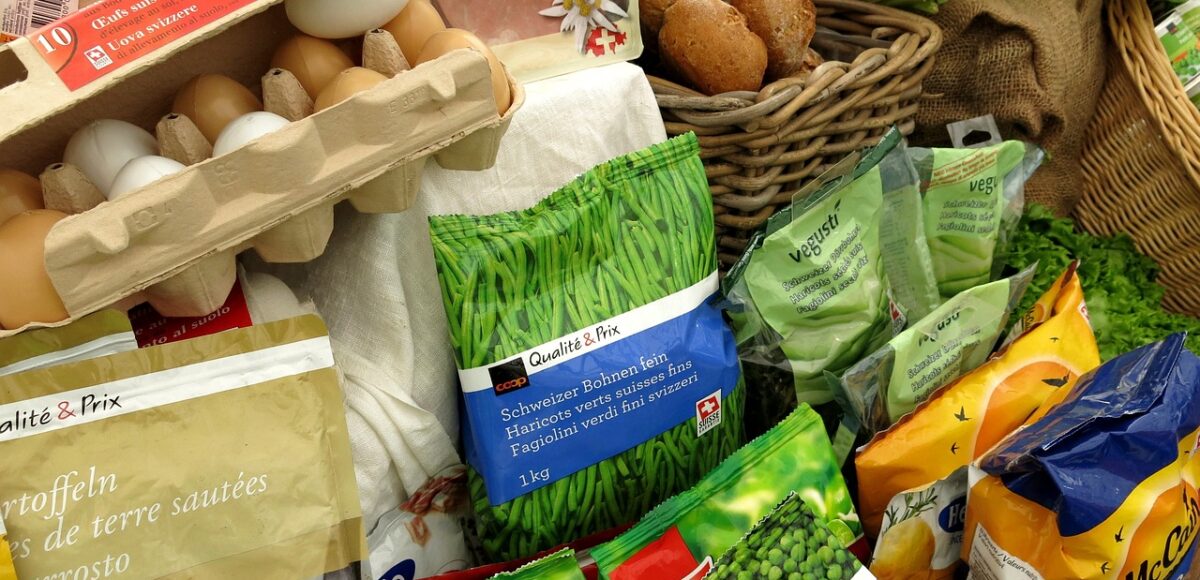
Laminating adhesive for flexible packaging
In this article, we will introduce the laminating adhesive for flexible packaging. In the past, packaging may not have been considered very important, but today various products are transported worldwide under different temperature conditions. Therefore, various criteria have been proposed for ideal packaging to ensure it demonstrates a minimum level of resistance against heat, cold, impact, and other damaging factors. One of the important features of packaging is flexibility. Typically, this type of packaging has a layered structure that is covered with laminating adhesive.
Flexible packages
Over time and with the increasing demand for products, the variety of packaging has significantly increased. Flexible packaging is considered a suitable option for various products because it offers greater resistance and strength compared to cardboard, metal, or inflexible packaging. Additionally, it is economically advantageous.
The process of placing one surface on another is called laminating. This process is used for flexible packaging, where layers of cellophane or flexible packaging film are laminated with solvent-based or solventless laminating adhesives based on the contents of the package. This type of packaging includes various layers such as aluminum foil, metallized film, polyester, paper, etc.
What types of packaging use laminating adhesive?
Laminating adhesive is applied as a layer on various types of packaging, including cardboard and plastic, which enhances the strength of the packaging. Laminating adhesives are available in two types: solvent-based and solventless. Laminating adhesives can make the product cover either transparent or opaque.
Packaging for food products such as puffed snacks, chips, smarties, chocolates, and others are among the most tangible applications of laminating adhesive. In addition to food products, laminating adhesive is also used in the packaging of many pharmaceuticals or highly sensitive products.
Types of laminating adhesives for flexible packaging
High performance: High-performance laminating adhesives aim to achieve one of the following objectives for packaging:
- High resistance to heat and chemicals
- Thermal and mechanical stability
Medium to high performance: This type of flexible packaging laminating adhesive is designed for two specific applications:
- Laminating film/aluminum and film/film for packages containing hot products.
- Another application for medium to high-performance laminating adhesives occurs when the packaging films contain a significant amount of laser additive materials.
Medium performance: The applications of medium-performance adhesives include:
- Laminates that include films containing metallized polyester or aluminum.
- Laminates that prevent air penetration into the packaging.
Standard performance: The standard type of laminating adhesive has numerous applications. An example of standard adhesive use is in laminates with metallized or transparent films.
Are laminating adhesives harmful?
In the past, flexible packaging was covered with a layer called polyurethane. Polyurethane contains free isocyanate monomers and is considered toxic. The risk posed by these monomers to food products is greater because they can form aromatic compounds when in contact with moisture from food. This process carries significant health risks, including cancer; however, the use of laminating adhesives has resolved food safety Issues.
Advantages and disadvantages of laminating adhesive for flexible packaging
Flexible packaging is covered with two types of laminating adhesives, and we will discuss the advantages of each separately. Some key advantages of solventless laminating adhesives include:
- Cost-effective equipment for production
- Lower energy consumption and environmental benefits
- Occupying less space for required equipment
- No vapor or odor emissions during production
Solvent-based laminating adhesives are very suitable and widely used for sterilized food product packaging. The advantages of solvent-based laminating adhesives include:
- High bonding strength and durability
- Usability in complex laminations
- Creating transparency on the packaging
- Enhancing the flexibility of the packaging
The disadvantages of solvent-based laminating adhesives include high costs for equipment procurement, excessive energy consumption, and high solvent usage. Solvent-based laminating adhesives require drying time after application on the packaging, which can be time-consuming. However, due to the numerous advantages offered by solventless laminating adhesives and their lack of harmful compound production when in contact with moisture from food products, they are widely used.