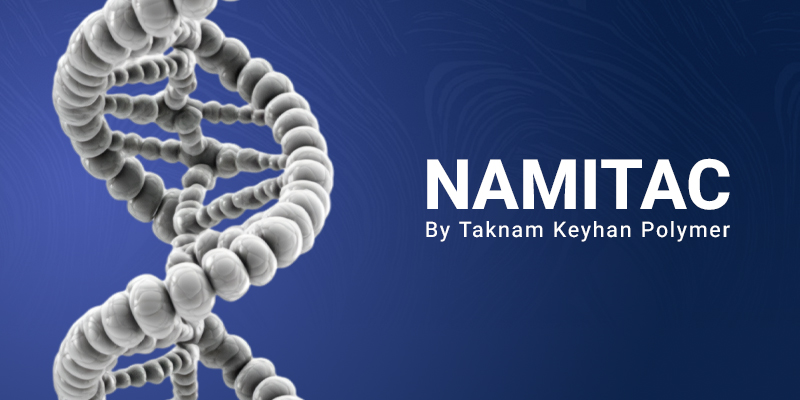
Specifications and properties of polyethylene film
Plastic films are lightweight, transparent, unaffected by biological factors, resistant to chemicals and weather conditions, printable, corrosion-resistant, shatterproof, and show resistance to temperature changes ranging from 60 to 200 degrees celsius.
In packaging terminology, plastic films are a thin and elastic layer of an organic material. Due to their low permeability, clarity, and smooth surface, they are among the most sought-after and reputable packaging materials.
The primary films used as packaging materials in the industry include: polyethylene (PE, LDPE, MDPE, HDPE), polypropylene (CPP, OPP, MOPP, BOPP, metallized films), polyamide, polyvinyl chloride (PVC), polyvinylidene chloride (PVDC), and polyethylene terephthalate (PET). These materials have different surface properties and can be used alone or in combination depending on product characteristics.
Polyethylene (PE)
Specifications and properties of polyethylene film: polyethylene is a thermoplastic film formed from the polymerization of gaseous ethylene monomer (CH2=CH2) under high pressure and temperature.
These transparent films are used more than other films in packaging printing and during the production of aseptic packaging boxes in a layered form. Polyethylene films are preferred especially for packaging fruits and vegetables, baked goods, pharmaceuticals, and in laminates and co-extrusions due to their characteristics such as durability and barrier properties, thermal sealability, and low cost. However, they do not have the clarity of polypropylene (PP) films.
Other essential features include:
- Clarity (cloudy/clear)
- Adhesion quality (thermal sealing)
- Surface tension
- Stiffness
- Impermeability (moisture/air)
- Surface additives (slip/anti-block/anti-static)
The most important point to consider when printing on polyethylene films is the drying of the ink on the surface. Since they are not absorbent, the drying of the printed ink layer on their surface occurs through evaporation; therefore, it is possible to print on plastic film surfaces with alcohol-based or specific solvent inks. The temperature of polyethylene film after printing decreases in the cooling section by 15 to 20 degrees Celsius. Since the surface tension forces of these films are generally low, there is no need for high temperatures or excessive tension during printing.
Polyethylene films are preferred based on density, molecular weight, and molecular weight distribution.
Density | Material | |
0,915 – 0,930 g/cm3 | (LDPE ) | Low-density polyethylene |
0,910 – 0,940 g/cm3 | (LLDPE) | Linear low-density polyethylene |
0,926 – 0,940 g/cm3 | (MDPE) | Medium-density polyethylene |
0,941 – 0,965 g/cm3 | (HDPE) | High-fensity polyethylene |
Low-density polyethylene (LDPE):
The properties of LDPE are similar to HDPE. However, LDPE has lower resistance to solvents and mineral oils. The thickness of the low-density polyethylene (LDPE) layer varies from 9 microns (as a tie layer in extrusion) to 0.25 mm (as a structural film). Key properties of the film include glossiness, resistance to various impacts, elongation, tear resistance and tensile strength, thermal sealability, ease of machinability, and printability.Low-density polyethylene (LDPE) is mainly used for plastic packaging films. It is very durable and transparent and has relatively low permeability to water vapor. Chemically, it is highly inert and virtually odorless and tasteless. One of its most significant advantages is that it can be easily bonded. For this reason, it is also used as an adhesive for creating thermal bonds in laminating applications. It has high tear resistance and is impact-resistant. Additionally, it features resistance to temperature changes from -50 degrees celsius to 70 degrees celsius.On the other hand, low-density polyethylene film has relatively high permeability to gases such as oxygen and carbon dioxide. Therefore, it is not very suitable for packaging that is prone to oxidation or for vacuum packaging as a direct film. It is also permeable to many types of oils. It should be examined whether some products packaged with low-density polyethylene experience gradual loss of odor and taste. They can be easily coated onto surfaces of materials such as paper, cardboard, and aluminum foil.LDPE film can be printed using flexo and screen printing methods. Low-density polyethylene is used for packaged bread, frozen foods, skim milk, sausages, chunk meat, and packaging bags.
Linear low-density polyethylene (LLDPE):
LLDPE has greater durability compared to LDPE and offers higher thermal resistance, but it is cloudier.
Medium-density polyethylene (MDPE):
MDPE film is tougher than LDPE, has a higher melting point, and provides a stronger barrier against water vapor. MDPE films are used when a structure is needed that softens more upon heating than LDPE or when these properties are required for use in another context.
High-density polyethylene (HDPE):
HDPE films have higher tear strength and tensile strength compared to paper and show good resistance to many acids, alkalis, alcohols, and other gases. Since it is not transparent, it is generally used in colored forms.High-density polyethylene is much stronger than LDPE, offers significantly better temperature resistance, and provides a greater barrier against water vapor. HDPE is 2 to 3 times less permeable to water vapor and gases than LDPE. HDPE films have higher tensile strength than LDPE but exhibit lower impact resistance. The highest temperature that HDPE can withstand is 120 degrees celsius, and its melting point is above the boiling point of water. Before reaching the point of relaxation or elongation, HDPE can withstand significant force (typically 210 to 280 kg/cm²).The barrier properties of HDPE films are also better and tougher than those of LDPE. The density of polyethylene is determined by its degree of crystallinity. An increase in crystallization means an increase in the order and frequency of molecular arrangement, resulting in higher polymer density. The resistance of the film to liquids and gases increases with density, as does its resistance to odor penetration.