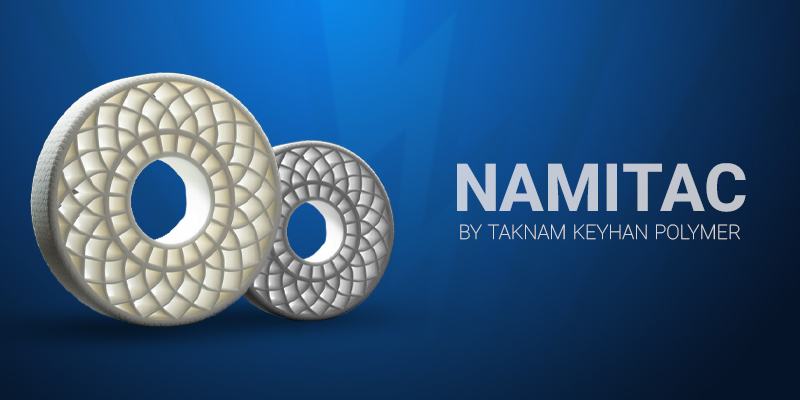
Polyurethanes: Flexible (Flex) polyurethane foam
Polyurethane, or polyurethanes, is a highly versatile material capable of solving many problems and is used in construction, furniture, bedding, automotive, bookbinding, and many other industries.
Because polyurethanes are durable, lightweight, and versatile, they can help reduce waste and lower energy consumption. Energy efficiency and recycling remain important topics that both industry and consumers face.
Polyurethanes are found in all aspects of building construction, from product manufacturing to meeting critical application needs on the job. They are used as insulation, adhesives, sealants, and foams in various building products and numerous other applications.
The desire and need for more energy-efficient buildings have encouraged increased use of polyurethane products.
Polyurethane or polyurethanes
Along with the rest of the plastics industry, the polyurethane industry supports methods to conserve resources and minimize the environmental and health impacts of plastics and plastic products. CPI advocates for the use of:
Environmental criteria and energy efficiency in product design and purchasing decisions, alongside product safety, cost, performance, and availability.
Flexible polyurethane foam (FPF) serves as cushioning for various consumer and commercial products, including bedding, furniture, automotive interiors, under carpets, and packaging. Flexible foam can be created in almost any shape and varying firmness. It is lightweight, durable, supportive, and comfortable. Flexible polyurethane foam accounts for about 30% of the total market and is primarily used in bedding, furniture, and the automotive industry.
What is flexible polyurethane foam?
Flexible polyurethane foam (FPF) is a polymer produced from the reaction of polyols and isocyanates, a chemical process that began in 1937. Due to this property, it is a preferred material in furniture, bedding, car seats, sports equipment, packaging, footwear, and carpet cushioning. It also plays a valuable role in sound insulation and filtration.
Foam is typically produced in large molds known as slabstock, which allows it to become a stable solid material that can then be cut and shaped into smaller pieces in various sizes and configurations. The production process of slabstock is often compared to rising bread – liquid chemicals are poured onto a conveyor belt and immediately begin to foam up as they rise into the shape of a large loaf (usually about four feet high) while moving along the conveyor. Raw materials for the foam can also be poured into aluminum molds where the foam takes on the size and shape of the mold. Molding allows for the production of foam items in shapes that are difficult to achieve otherwise.
The molding process can integrate foam components with other parts such as a metal frame. One example of this is the headrest of a car seat. Due to the high initial costs of producing molds, molding is usually reserved for high production runs. Molded foam is often found in automobiles, commercial furniture, and sports equipment.
Raw materials for FPF are often complemented with additives that impart desired properties. These range from comfort and support needed for upholstered seating to cushioning used to protect packaged goods to long-lasting abrasion resistance required for carpet cushioning.
Amine catalysts and surfactants can alter the cell size produced during the reaction of polyols and isocyanates, thereby changing the properties of the foam. Additives may also include flame retardants for use in aircraft and automobiles and antimicrobials to prevent mold growth in outdoor and marine applications. Once the foam is produced, it can be shaped into complex forms. The primary tools for foam fabrication – vertical band saws and horizontal slitting – are adapted from woodworking machinery. Since flexible foam can be connected to a cutting blade configured on a rotary wheel, a process known as ring slitting can be employed.
Manufacturers also utilize lasers, hot wires, water jets, wave twisting, and other technologies. Foam can be compressed during cutting to create effects such as ” convoluted” foam that is sometimes used in mattress toppers.
Polyurethane can also be combined with other materials such as non-woven substrates, mesh, fabrics, and fibers. Bonding techniques include flame bonding, hot film bonding, hot melt adhesive bonding, and powder layering, where powdered adhesive is used to bond the foam to the substrate through a thermal process. Headliners (the padded ceiling inside vehicles) are typically made from a non-woven fabric that is bonded to the backing of thin foam using flame bonding.
Other processes alter the structure and performance characteristics of the foam. One of the most striking and beneficial changes is crosslinking. Crosslinking involves breaking many of the cell walls of the foam to create increased porosity and airflow. This can be achieved by exposing the foam to a controlled explosion of a gas mixture in a closed reactor or by placing the foam in a burning bath. Crosslinked foam is often used in air and fluid filter systems and as anti-slosh membranes in fuel tanks.
One of the most important commercial formulations of foam involves processing foam waste into bonded carpet cushions. Scrap foam of various types is shredded and placed in a processing unit with a chemical adhesive. The mixture is then compressed and injected with steam to form a large cylinder or block of foam. This material is then shaved down to appropriate thicknesses for use as carpet cushion. Bonded foam is the most popular type of carpet cushion, accounting for over 80 percent of the market share.