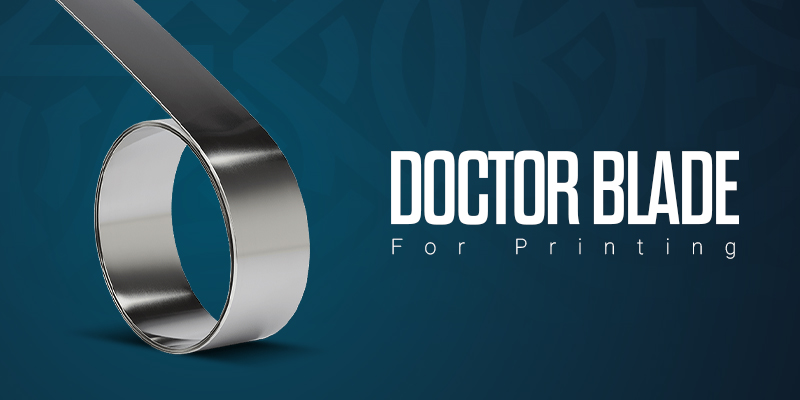
Introduction to doctor blade for printing
The doctor blade, also known as a metering blade, is a tool used in various industries, particularly in printing and coating applications. It is a thin, flat strip made from metal, plastic, or composite materials that is used to remove excess ink, coating, or other liquids from a surface.
What is a doctor blade?
A doctor blade is a thin, flat rod made from various materials such as polymers, steel, or micron that is used in the printing and packaging industry to remove excess ink or coating from the surface of a printing plate or cylinder. It is positioned at an angle against the printing plate or cylinder and then moves across its surface, removing excess ink or coating and leaving a uniform layer of ink or coating on the surface. The pressure applied to the blade and the angle at which it is held are important factors in determining the amount of ink or coating that needs to be removed. The doctor blade plays a vital role in ensuring the highest quality print output by removing excess ink or coating from the surface of the printing plate or cylinder and providing consistent, high-quality print results.
The primary purpose of the doctor blade is to control the amount of ink or coating applied to a substrate and ensure a precise and consistent coating. Its operation involves removing excess liquid from a rotating cylinder or roller, such as anilox roll in a printing machine or a coating roll in a coating machine. By controlling the thickness of the liquid film remaining on the surface, the doctor blade helps achieve the desired print quality or coating thickness.
This is typically positioned at a slight angle relative to the surface being treated. This angle, known as the doctoring angle, allows for controlled removal of excess liquid without damaging the roller or cylinder. The blade may be adjusted or replaced to achieve optimal results based on factors such as ink viscosity, roller speed, substrate type, and desired coating thickness.
In printing, the doctor blade removes excess ink from the smooth and engraved areas of the anilox roll and the ground regions of the cell walls. doctor blades are also used in other printing and coating processes, such as flexographic printing. In a single-blade ink system or dual-blade ink system, the Doctor Blade separates excess ink from the cylinder or anilox roll to create a uniform layer of ink to be transferred to the printing plate. The blade/anilox combination is designed so that (primarily) it is the blade that wears out, not the anilox roll. The doctor blade is a relatively inexpensive and disposable consumable, while the gravure cylinder or flexo anilox is a more expensive component of the press. Common materials for doctor blades include steel or polymer.
How does a doctor blade work?
The doctor blade works by applying pressure to the surface of the printing plate or cylinder, removing excess ink or coating while leaving a uniform layer of ink or coating on the surface. The doctor blade is positioned at an angle to the printing plate or cylinder that typically ranges from 30 to 45 degrees and then moves across its surface. As the blade moves, excess ink or coating is removed while leaving a thin, uniform layer of ink or coating behind.
The pressure applied to the blade and its holding angle are crucial factors in determining how much ink or coating is removed. If the pressure is too high, the blade may damage the printing plate or cylinder; if it is too low, the doctor blade may not remove enough ink or coating, resulting in lower print quality.
Additionally, the performance of the doctor blade is influenced by its material and design. Different types of doctor blades, such as polymer, steel, or micron blades, have varying wear resistance and flexibility properties that make them suitable for specific printing applications. Furthermore, the design of the doctor blade, including thickness, bevel angle, and tip radius, can affect its effectiveness in removing ink or coating from the surface of the printing plate or cylinder.
- Steel doctor blade:
Steel boctor blades provide excellent durability and wear resistance but can be prone to wear over time due to their rigidity.
- Polymer doctor blade:
Polymer doctor blades are made from flexible plastic materials such as polyurethane or polyester. They offer good wear resistance, high flexibility, and excellent compatibility with the printing plate surface. Polymer doctor blades are suitable for applications requiring high-quality print output and reduced wear on anilox rollers.
- Micron doctor blade:
Micron doctor blades are similar to steel blades but are much thinner, typically ranging in thickness from 20 to 40 microns. They are made from hard stainless steel and offer excellent blade life, wear resistance, and stability.
It is suitable for applications that require fine line printing, high-quality graphics, and precise images.
- Ceramic doctor blade:
Ceramic doctor blades are made from high-strength ceramic materials and offer excellent wear resistance, durability, and chemical resistance. They are suitable for applications that require aggressive ink removal, such as printing on heavy cardboard or metal surfaces.
In summary, the most common types of doctor blades are steel, polymer, micron, and ceramic. The choice of the appropriate doctor blade type depends on the specific printing application requirements, such as print duration, print quality, and substrate type.
The most important point in selecting a doctor blade for printing is its flatness. These blades are typically secured in place with a fixed assembly at the appropriate angle. The friction or premature wear of the blade depends on the following factors: the presence of foreign particles (dust), coarse pigment particles in the ink, excessive fatigue or corrosion, excessive pressure and breakage, oxidation or rusting due to inferior ink, as well as the low quality of the blade.
( 40 * 200 * 1.7 * 0.125) | A * B * C * D |
A = Blade width (millimeters) | |
B = Blade thickness (microns) 200 and 150 microns | |
C = Edge width (millimeters) | |
D = Edge thickness (millimeters) |
Method of installing the doctor blade for printing on the machine:
To understand the impact of a material’s properties in a doctor blade, it is necessary to consider the application, i.e., the environment in which the material will experience use.
In flexographic printing, the doctor blade comes into contact with two other main components: the anilox roll and the printing ink. The former provides an abrasive surface, often significantly harder than the doctor blade, while the latter provides abrasive particles (ink pigments) in a liquid suspension. This liquid may chemically interact with the doctor blade if the two do not match chemically.
Essentially, the surface roughness of both the doctor blade and the anilox roll collectively contributes to print quality, as the precision of operation depends on the contact between these two.
Thoroughly clean the base body and metal guard and apply a very small amount of oil or grease. Then, while observing all safety precautions and with utmost care, select a suitable blade to match the length of the body and place it under the metal guard. Leave approximately 20 millimeters of guard from the edge of the body and 3 to 4 millimeters of blade extending from the edge of the guard, then slightly tighten the screws. When fully tightening, start with the middle screw using the appropriate wrench towards the edges, and then completely tighten one from the left and one from the right.
If the blade edge appears wavy, carefully open and close it again to avoid issues during operation. To ensure print quality during blade installation, be attentive and allow sufficient time.
Flexo doctor blade system:
Rotogravure doctor blade system:
Ensure accuracy in adjusting pressure and angle to prevent breaking and premature wear of the blade and cylinder. Typically, set pressure between 1.5 to 2 bars and angle between 55 to 65 degrees for gravure and 30 to 35 degrees for flexo.