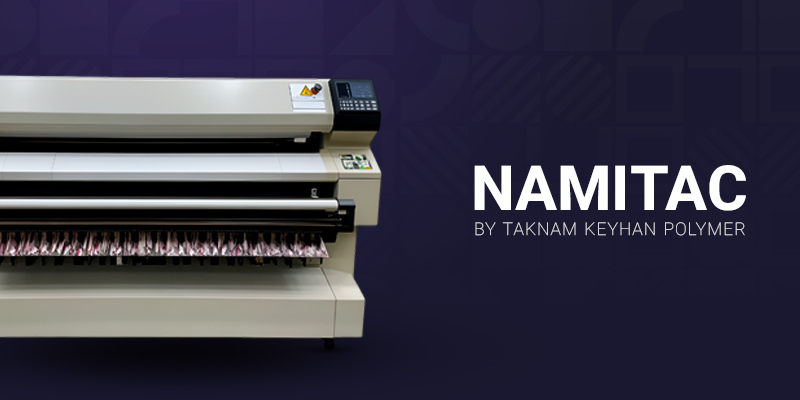
Familiarity with different printing methods
Classifying printing methods into a few specific groups allows us to gain a clear understanding of the concept of printing and the structure of all printing devices without getting lost in the various types of machines and their differences in dimensions, applications, auxiliary equipment, and levels of automation.
Major printing methods: There are many diverse methods for printing on paper, various materials, and different objects, with a range of small and large machines invented and used for specific tasks. Despite the vast variety of devices, supplies, and techniques related to printing for each of the above items, printing methods can be broadly classified based on the form of printing and the way ink is transferred into the following categories:
A) Contact printing group: The division of printing methods into contact and non-contact categories is relatively recent. This term was coined when new printing methods were developed that perform printing without the printing surface coming into contact with the printing form (or printing medium), which could be referred to as non-contact in comparison to traditional methods. In fact, all printing methods that fall under the contact printing category are traditional printing methods and the primary techniques for producing printed works that have been around for years and are still recognized as major printing methods. Contact prints are divided into four groups based on the type of printing form and the method of ink transfer:
- Relief, such as letterpress and flexography
- Intaglio, such as gravure and pad printing
- Flat, such as offset and lithographic printing
- Screen, such as silk screen and stencil
B) Non-contact printing group: This term relates to more recent types of printing, including toner systems (like photocopying, which uses powder instead of liquid ink) where there is no printing form or intermediary for transferring ink onto paper or the printing surface. Ink transfer occurs based on a specific pattern and method at designated points. Non-contact printing is generally divided Into two groups:
- Electrostatic (such as photocopying and toner digital printing)
- Inkjet (such as desktop inkjet printers, plotters, and large format printers).
Typically, offset printing allows for printing on all materials, including paper, while silk screen printing is used for cans. Printing on pens or mobile phone buttons can be done using both silk screen (screen) and pad print (intaglio) methods. Expiration dates printed on beverage caps and milk bottles represent a basic form of inkjet printing, while billboard printing is a more advanced version.
Offset printing typically uses powder, and fancy or relief prints like thermography are usually performed using heat. Notably, we should mention offset letterpress machines. In these machines, the printing form is raised; however, since ink transfer occurs through a rubber cylinder, it is considered offset. The combination of these two is referred to as offset letterpress. This overview of printing methods is comprehensive up to this point, but it can be expanded further.
Types of cellophane printing methods:
-
Gravure printing (intaglio):
Gravure is a type of printing that historically involved lead type. It uses a metal cylinder where ink is transferred through engraving onto the work. In gravure printing, ink is applied through holes in the work, with each print having its own specific cylinder. Gravure has higher pre-printing costs; making cylinders is time-consuming but they last longer. Since it is used for high-volume print runs, costs are distributed over larger quantities, resulting in greater print precision.
-
Flexo printing:
Flexo printing utilizes a relief surface similar to the spikes on sports shoes through which ink is printed onto the work. Creating plates (like gelatin stamps) in flexo requires less time and is cost-effective for lower print runs. There are three types of flexo: line flexo, central cylinder, and stack flexo.
The intensity of the print (boldness or lightness) is determined by the size of the relief holes. The main difference in quality and speed between gravure and flexo printing is significant. Typically, polyethylene film is printed using flexo. Since gravure is used for high-volume runs and requires more diverse and expensive equipment, large printing complexes in the country that hold a major share of cellophane printing mostly use high-quality solventless adhesives that have low grammage and do not cause problems in machines while being compatible.
In cellophane printing, UV ink is used, meaning it dries with light. Companies that produce polyethylene film typically work with flexo printing.
In any case, the discussion of various issues related to printing technology, applications, consumables, as well as historical analysis and other printing matters can be expanded based on this general classification. For example, we can talk about the preparation or pre-printing methods for each of these techniques, similarly regarding post-printing operations, and we can also investigate the applications and consumables used in each method.
We can also look at printing methods from the perspective of technical and economic justification for carrying out a particular printing order, thus finding a variety of points across different branches of the printing tree. Pre-printing (preparation) encompasses all printing methods, which have a stage called pre-printing before the printing phase. The set of operations that occur after layout and artwork preparation or after executing the design, in order to prepare that work for printing, is considered pre-printing. The final stage before printing is the preparation of the plate (or the form ready for printing).
The impact of corona on flexible packaging film lamination
“Pre-printing” in its broadest sense includes typesetting and design, while in its specific sense refers to the preparation of the printing form or operations that lead to the production of the plate. Preparation in all printing methods has traditionally had its own specific stages, operations, and consumables, and today it is gradually being replaced by digital preparation. The main operations and stages of conventional preparation in all methods include: photography, color separation, film creation, form setting, and copying. In digital preparation, all operations of photography, retouching, and form setting are carried out using pre-press software on computers, and plate generation is done through computer systems, eliminating the film production stage and complex film creation operations. Nevertheless, whether preparation is traditional or digital, at its conclusion, plates or printing forms are produced that are ready to be installed in the printing machine for duplication. The three main and widely used devices in preparation centers are: scanner, imagesetter, and plate setter.
The preparation stages for each of the printing methods are as follows:
- Lithography: Preparation for offset printing, with the final product being zinc.
- Stereotyping: Preparation for flexo printing, with the final product being photopolymer plates.
- Cylinder creation: Preparation for gravure printing, with the final product being an engraved copper cylinder.
- Stencil making: Preparation for silk screen printing, with the final product being a stencil (mesh).