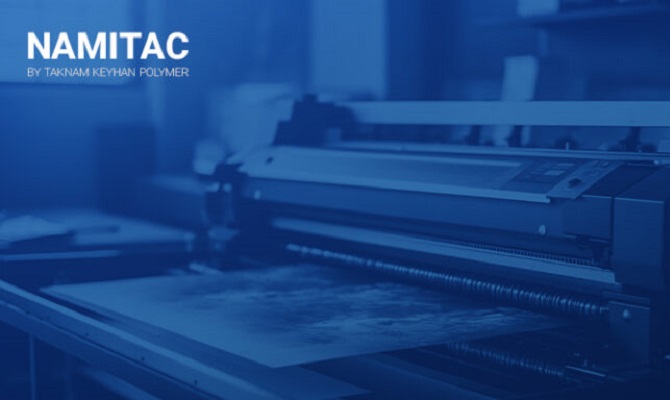
Types of lamination methods in flexible packaging
The achievement of multilayer structures has enabled us to enhance the application of plastic materials for food packaging. Sometimes, there is no single material that meets all the requirements necessary to preserve a product. Therefore, combining different materials with varying properties and functionalities makes it possible to provide an optimal structure for packaging.
What is lamination?
Lamination is a process through which two or more flexible packaging films are bonded together using a bonding agent. Essentially, lamination is a process of joining two or more layers of materials together to create a single composite structure. It involves applying a laminating adhesive, usually in liquid form, between the layers and then applying pressure or heat to create a strong bond. The substrates that make up the films may consist of various materials such as films, papers, or aluminum foils, depending on the desired properties of the final product. Films are commonly used materials for multilayer packaging.
Lamination is widely used in various industries, including flexible packaging, graphic arts, construction, automotive, and electronics, to enhance the strength, durability, appearance, and performance of materials. This process offers several advantages, including improved barrier properties, increased stiffness, resistance to moisture, protection against abrasion and tearing, and customization options.
The impact of corona on flexible packaging film lamination
The lamination process can be carried out using various techniques such as wet lamination, dry lamination, thermal lamination, extrusion lamination, or flame lamination, depending on the specific materials and requirements. The choice of lamination method depends on factors such as the materials being laminated, the desired bond strength, production speed, and the intended application of the laminated product. In flexible packaging, dry and wet lamination, extrusion lamination, solvent-based lamination, and solvent-free lamination are commonly used.
Lamination is extensively used in applications such as multilayer packaging (e.g., bags, pouches, and wraps), multilayer flooring, multilayer signs and banners, multilayer ID cards, laminated documents, multilayer furniture components, etc. It provides better performance, protection, and visual appeal for materials, making them more durable and versatile for various applications.
In solvent-based lamination, the only thing that remains on the support unit is the solid part of the resin adhesive that has an initial tackiness allowing it to be pressed onto another support element after exiting the tunnel. This Initial tack prevents slipping of the attached supports. The combination of both supports is rolled up and maintains a certain pressure between the layers to ensure good contact and a strong final bond between them.
What is solvent-based laminating adhesive?
The crosslinking reaction of the laminating adhesive progresses over time, increasing bond strength; it is necessary to allow at least 24 hours before achieving a satisfactory bond so that the production process (rolling and cutting) can continue.
Types of lamination methods in flexible packaging
In packaging, various lamination processes are employed to achieve specific functions and characteristics. The different lamination methods are classified as follows:
- Thermal and pressure lamination or dry lamination: Also known as dry bond lamination, this method uses heat and pressure to bond layers together using a pre-applied adhesive. In this process, a heat-activated adhesive, usually in liquid or powder form, is applied to one of the layers. The layers are then passed through heated rollers that activate the adhesive and bond the layers together. Dry lamination is typically used for plastic film-to-film or film-to-paper applications. One substrate must be a good conductor of heat while the other can be a plastic layer such as polyethylene that has been corona-treated.
- Wet lamination: Also known as wet adhesive lamination, this method involves using a liquid adhesive to bond two or more layers together. The adhesive is applied to one of the layers, and then the layers are pressed together to form a bond. Wet lamination is often used for paper-to-paper or paper-to-film applications, such as book covers, brochures, or labels.
- Adhesive lamination: A process in which a solution or emulsion of low molecular weight polymeric adhesive material is applied to the surface of one substrate before being bonded to a second layer is typically referred to as adhesive lamination.
- Hot melt lamination – the molten wax is applied to the substrate in a roller coating process, and the other substrate is laminated under pressure from the rollers and immediately passes over a cooling roll. The saturation of the adhesive is achieved by fully immersing the substrate in a tray of molten adhesive. Wax-coated papers or multilayered or impregnated papers are widely used in the biscuit and confectionery industry.
- Extrusion coating lamination – this involves bonding two or more layers together using a molten polymer. In this process, a molten polymer film is extruded between two substrates, usually flexible layers. This thin layer is then applied to another substrate and immediately passed through a cooled roller to form a strong bond and is wound into rolls. Extrusion lamination is commonly used in flexible packaging applications such as snack food bags, stand-up pouches, and multilayer films.
- Solventless lamination – this is a process in which the laminating adhesive is applied to the surface of one substrate and then bonded to another substrate under pressure. Unlike wet lamination, solventless lamination does not require the use of solvents. This process is widely used in flexible packaging applications and ensures high bond strength and increased stability due to the absence of solvents.
Suitability for packaged products inside:
The lamination process is chosen for various products based on the characteristics of the packaged product on the side. Solventless lamination is suitable for various juice packaging and some packaging where ethyl solution is not required, making it appropriate for ready-to-eat products and lightweight products. Extrusion lamination is used for all bulk product packaging that requires greater strength in the lamination. In types of woven BOPP laminated bags, we will use extrusion lamination. Wet lamination is used where one of the laminated substrates is paper or any porous substrate and is suitable for various lightweight product packaging.
Overview of the history of the flexible packaging laminate adhesive industry
It is very important to carefully evaluate your specific project requirements and considerations before selecting a lamination method. The limitations of wet lamination, such as longer drying times, potential adhesive ooze, unsuitability for certain materials, environmental considerations, and limited durability under specific conditions, make it less competitive.
Laminated films and lamination methods in flexible packaging
Laminated films produced through various lamination processes exhibit different properties and characteristics. Each lamination process, such as dry lamination, extrusion lamination, or solventless lamination, imparts specific features to the resulting laminated film.
Lamination techniques Residual solvent | Brittleness (film rigidity and flexibility) | Clarity | Oil resistance | Heat and water resistance | Coating amount (GSM) | Residual solvent |
Solventless lamination | Excellent | Excellent | Excellent | Excellent | 0.8-2 g | Excellent |
Dry lamination | Good | Good | Excellent | Excellent | 1.8-5 g | Poor |
Extrusion lamination | Poor | Good | Good | Good | Good | |
Wet lamination | Poor | Poor | Good | Good | 2-6 g | Excellent |
Advantages and disadvantages of lamination processes
Each lamination process has its own strengths and weaknesses, which can vary depending on the application and specific needs. Here are some general advantages and disadvantages of lamination processes:
Laminate techniques and methods | Advantages | Disadvantages |
Solventless lamination |
|
|
Dry lamination |
|
|
Extrusion lamination |
|
|
Wet lamination |
|
|
It is important to note that these advantages and disadvantages are general observations and may vary based on specific materials, adhesives, and processing parameters involved in each lamination method.