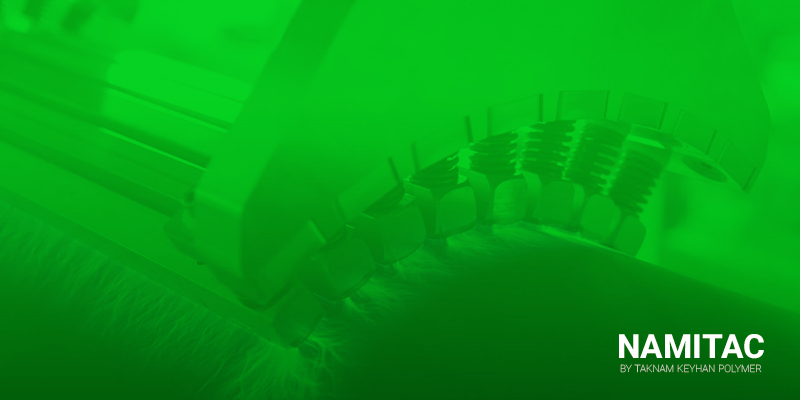
The impact of corona on flexible packaging film lamination
Basic principles of corona treatment
Corona treatment is a type of electric shock treatment that enhances the adhesion of the substrate surface. The purpose of corona treatment is to alter the surface energy of various substrates and facilitate their bonding with printing inks, coating materials, and laminating adhesives.
A corona device is a capacitor that creates a layer of ionized air regardless of the type of film passing through it, and it has the capability to make films hydrophilic and ready for converting. Most plastic films (such as polypropylene films) are non-polar polymers with low surface tension. Printing inks and laminating adhesives cannot adhere strongly to them. Therefore, the surface must be treated with corona to break down the chemical bonds of the plastic molecules, increasing roughness and surface area.
In general, corona performs several functions on the surface of flexible packaging films. It forms low molecular weight materials on the surface of the film, oxidizes the film surface, and creates positive and negative charges by adding and removing electrons. Corona cleans the film from organic and inorganic contaminants that interfere with laminating adhesive performance. Corona treatment can lead to microscopic changes and an increase in the surface area of the film, resulting in a higher likelihood of successful adhesion.
The best way to measure the effectiveness of surface treatment is to complete all operations and measure the level of adhesion. A quick test to monitor changes on the surface after treatment is the dyne test.
Dynes are units of measurement that assess the surface energy of films. Three important points to remember when applying different dyne levels are:
First, dyne results depend on the proper execution of the test and its variations. A deviation of at least 2 dynes is very likely. Second, measuring dyne before and after treatment only covers a small portion of the film. Finally, achieving the ideal dyne level does not guarantee adhesion. Observing varying adhesion results from films with the same dyne levels Is not uncommon.
Low corona solutions for films
Low corona levels for films (below 36 dynes for solvent-based laminating adhesives and 40 dynes for water-based laminating adhesives).
If possible, re-corona treat films until acceptable surface energy is achieved. Using freshly corona-treated films is desirable. However, it is recommended to corona treat films with a density of 1 watt to ensure a clean laminate surface. For older films or those that have not been corona treated previously, a higher watt density is required. Corona treatment is recommended to achieve 36 dynes per centimeter for solvent-based laminating adhesives and ideally 40 dynes per centimeter for solventless and water-based adhesives.
Increase surface polarity with active groups (carbonyl, hydroxyl, hydroperoxide, aldehyde, ether, ester, carboxylic acid, etc.).
Remove surface contamination from the film.
In the lamination process, printed and laminated films should be treated before printing and laminating. An inline corona treatment operation is recommended as it has a cleaning effect and improves ink adhesion on the substrate.
Surface tension is measured using a contact angle device or test pens.
Impact of corona treatment on bond strength values:
Corona treatment in-line before printing improves adhesion and bond strength in lamination.
In tropical countries, humidity (relative humidity) also reduces the efficiency of corona treatment (water molecules interact with functional groups on the polymer surface (carboxylic acid, hydroxyl, etc.)).
Applied corona is related to:
- Film nature
- Film speed
- Desired final surface treatment
Older films require more energy for treatment due to the presence of slip agents.
Example: In PET films, surface tension should be 52 dynes/cm. The corona treatment should be low so as not to damage gas permeability properties.
This diagram illustrates the impact of corona treatment on the adhesive strength of films with polyvinyl butyral ink.
Secondary corona treatment of films
After initial corona treatment, the network structure of the film’s surface layer and packaging wrap is less than that of the internal bonding layer; therefore, functional groups on the surface layer have greater mobility. Consequently, the corona treatment of many wraps decreases over time (e.g., after more than one year).
In this case, secondary corona treatment is needed, which can remove dirt from the surface of the film and not only helps improve the adhesion of the printing ink but also enhances the visual appeal of the printed and laminated packaging.
Summary
The first step in understanding the relationship between the film and corona operations is to remember that the corona device is unable to comprehend how the film reacts to the treatment, and each film has a unique response to the process. Ultimately, it depends on your process to discover and document how different levels of treatment can greatly contribute to achieving the goal of “maximum adhesion.”